Oakley x US Military
The Challenge:
The US Military requested development of a desert combat boot that could withstand the rigors of Fast-Rope deployment, the hazards of urban warfare and the climate of desert combat. It needed to be breathable, flexible, durable and adhere to the Military's strict code of construction and aesthetics.
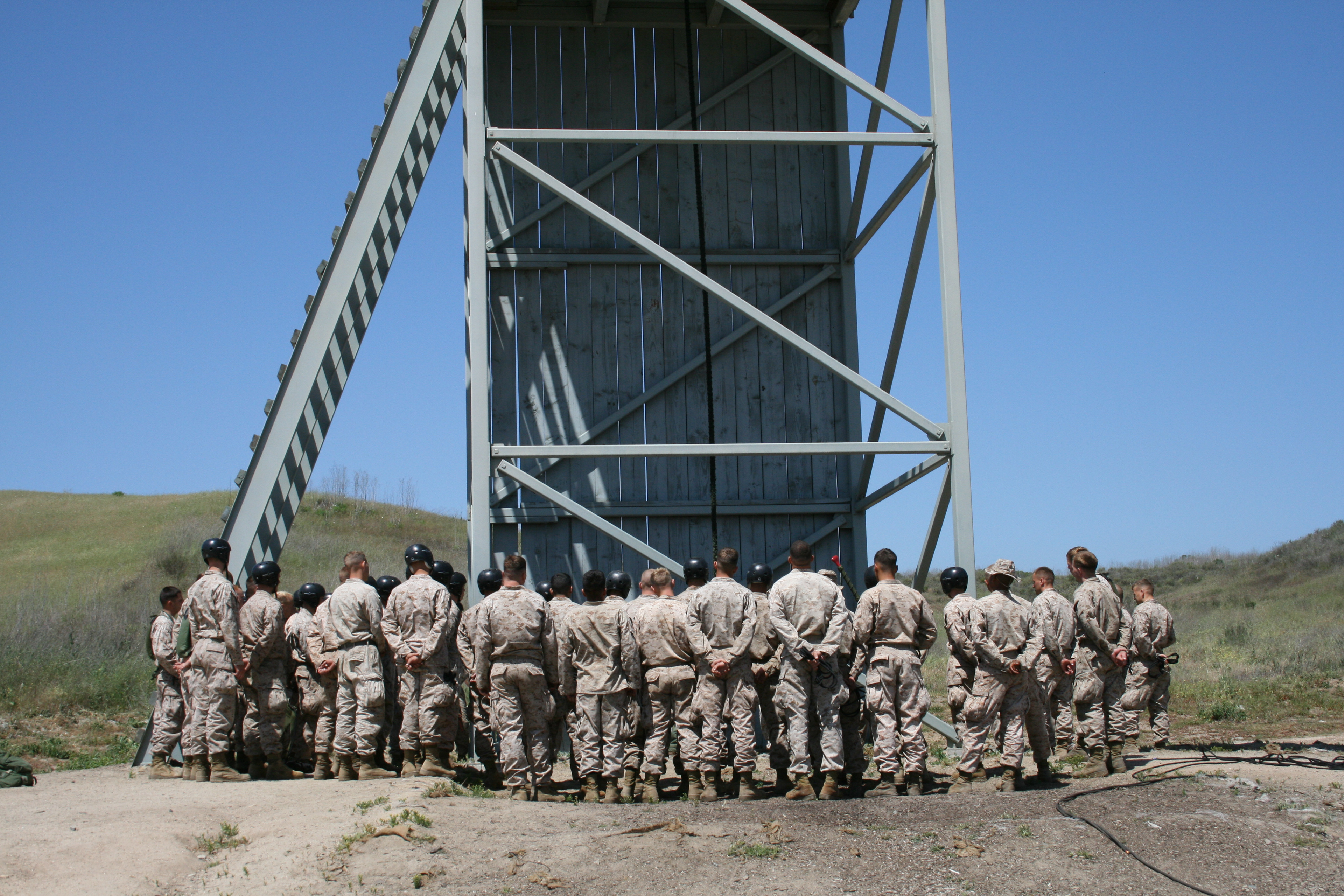
Research and development took place at Camp Pendleton to observe how soldiers were trained and what rigors their equipment went through.
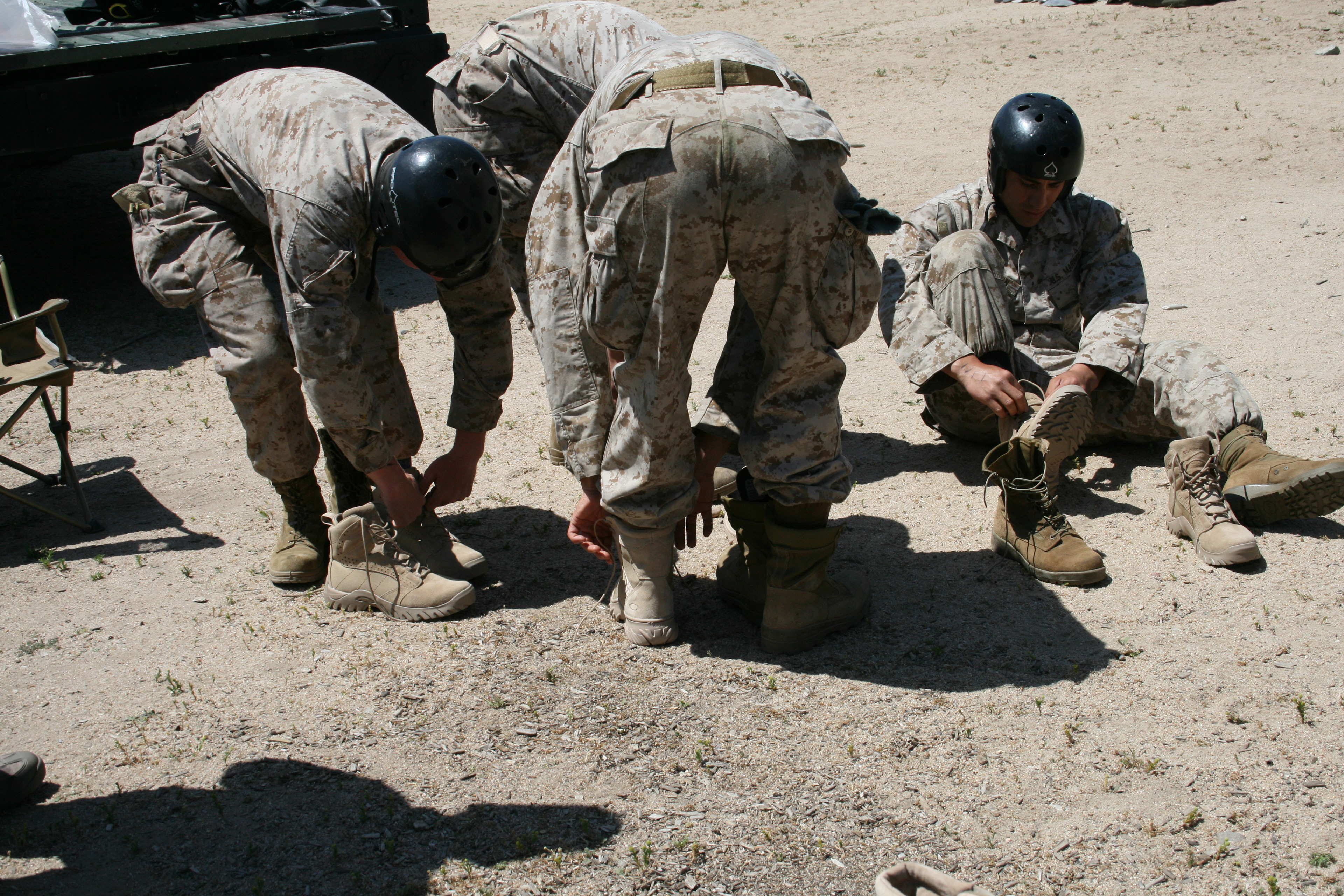
We had them do trial runs on their standard issue boots.
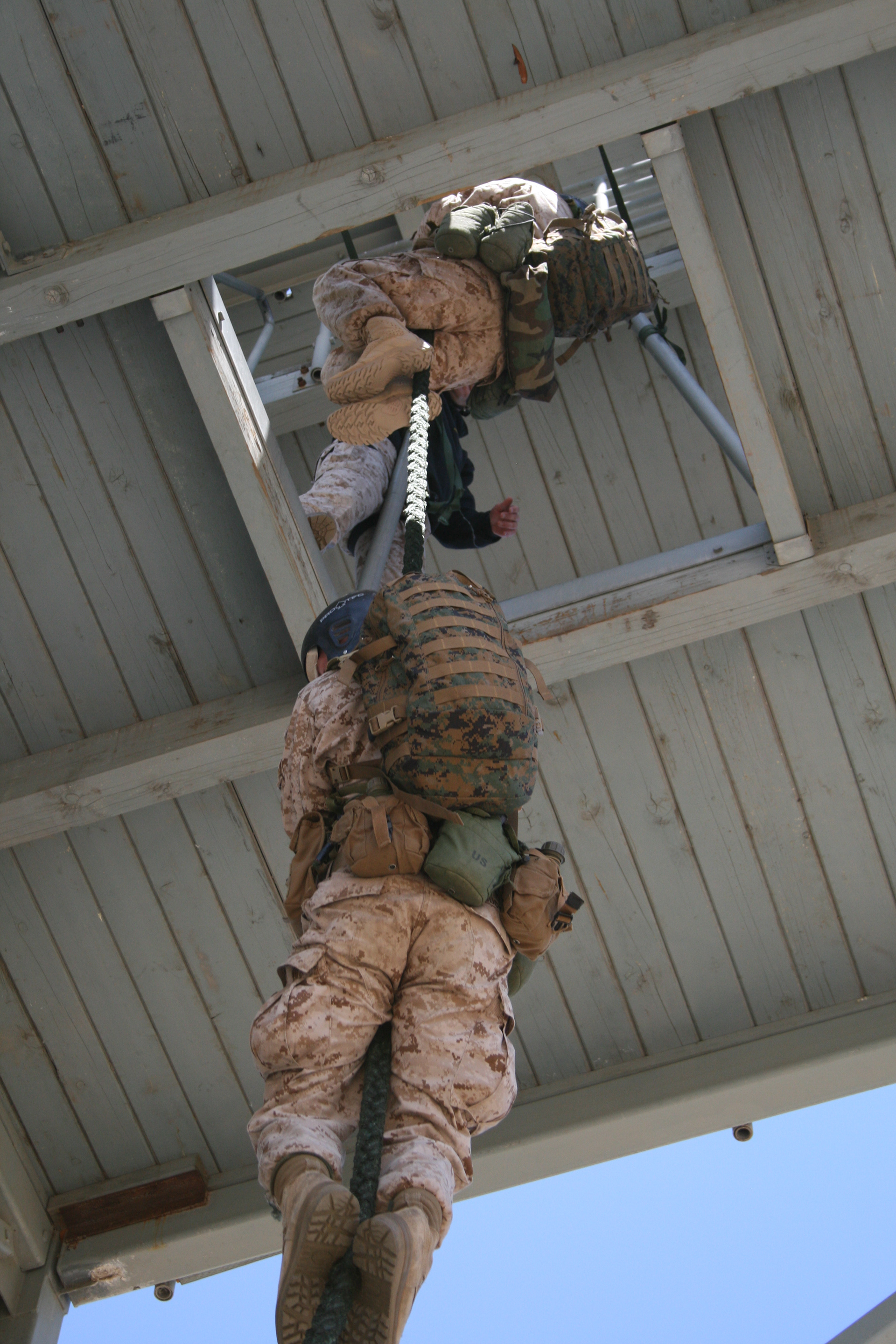
Soldiers had to train on the Fast Rope with backpacks and equipment that weighed 70 lbs and up. They had to be able to control their descent with their gloves as well as their boots.
Our first stop was Camp Pendleton. We needed to see how soldiers trained, what they put their footwear through and listen to what they needed to help them perform their best.
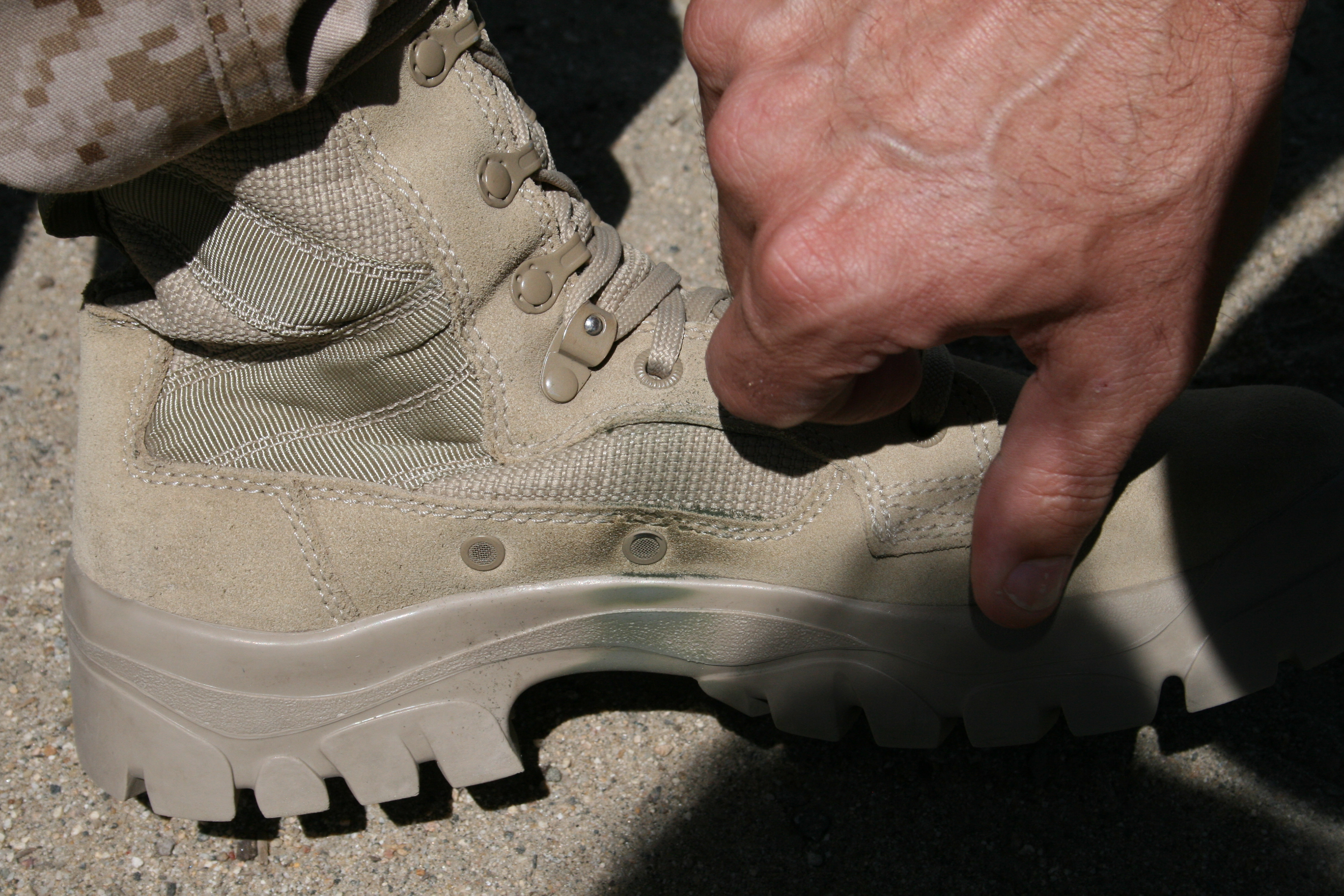
We noted what happened to the medial side of the standard issue boot after just one Fast-Rope run. The leather and fabric started wearing and the stitching started to fray.
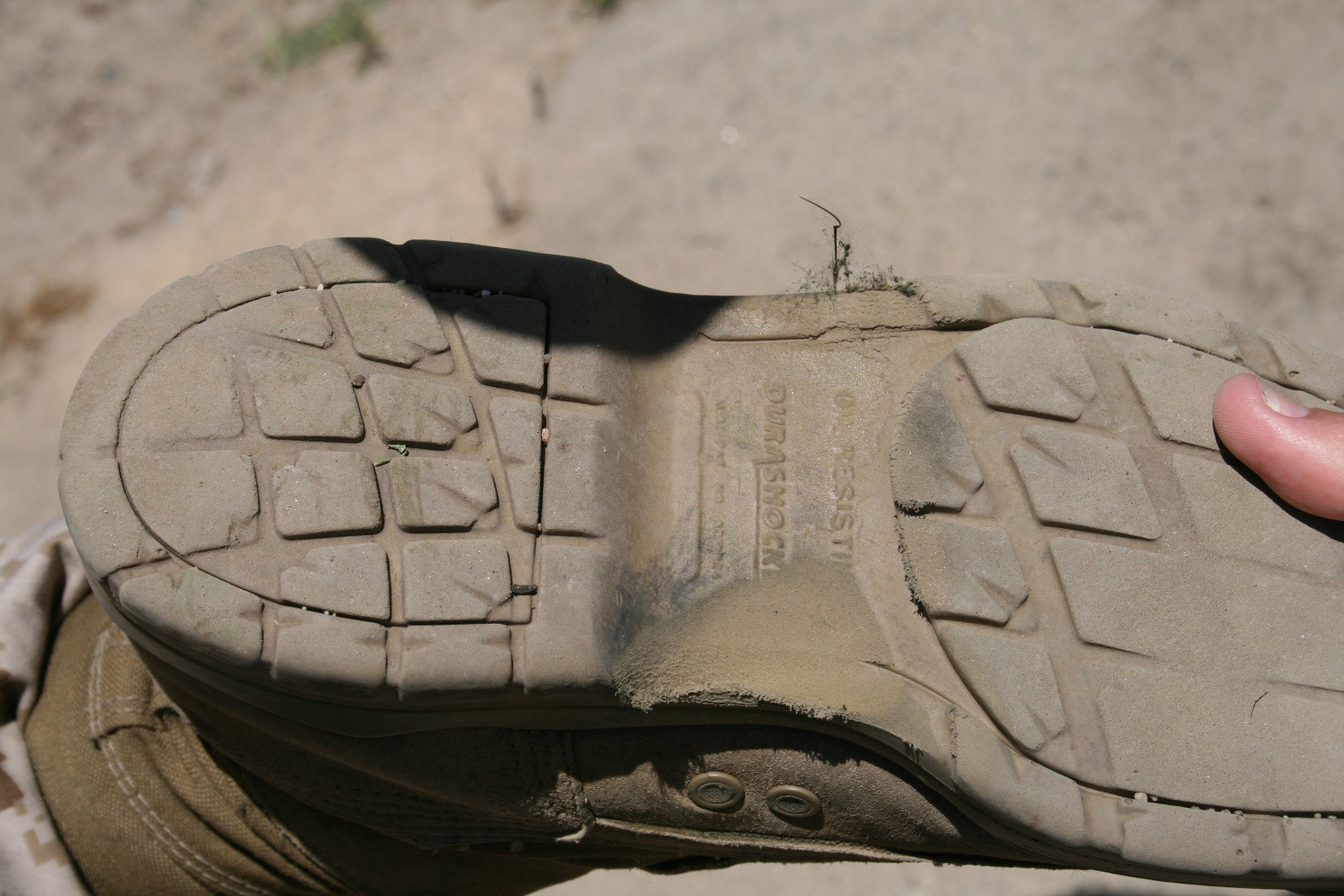
After 3 Fast-Rope runs we understood why we were asked to develop a new Fast-Rope capable boot. The rubber on the standard issue boots wore out quickly when they were used to slow down a standard 200 lb soldier and their 70 lb backpack.
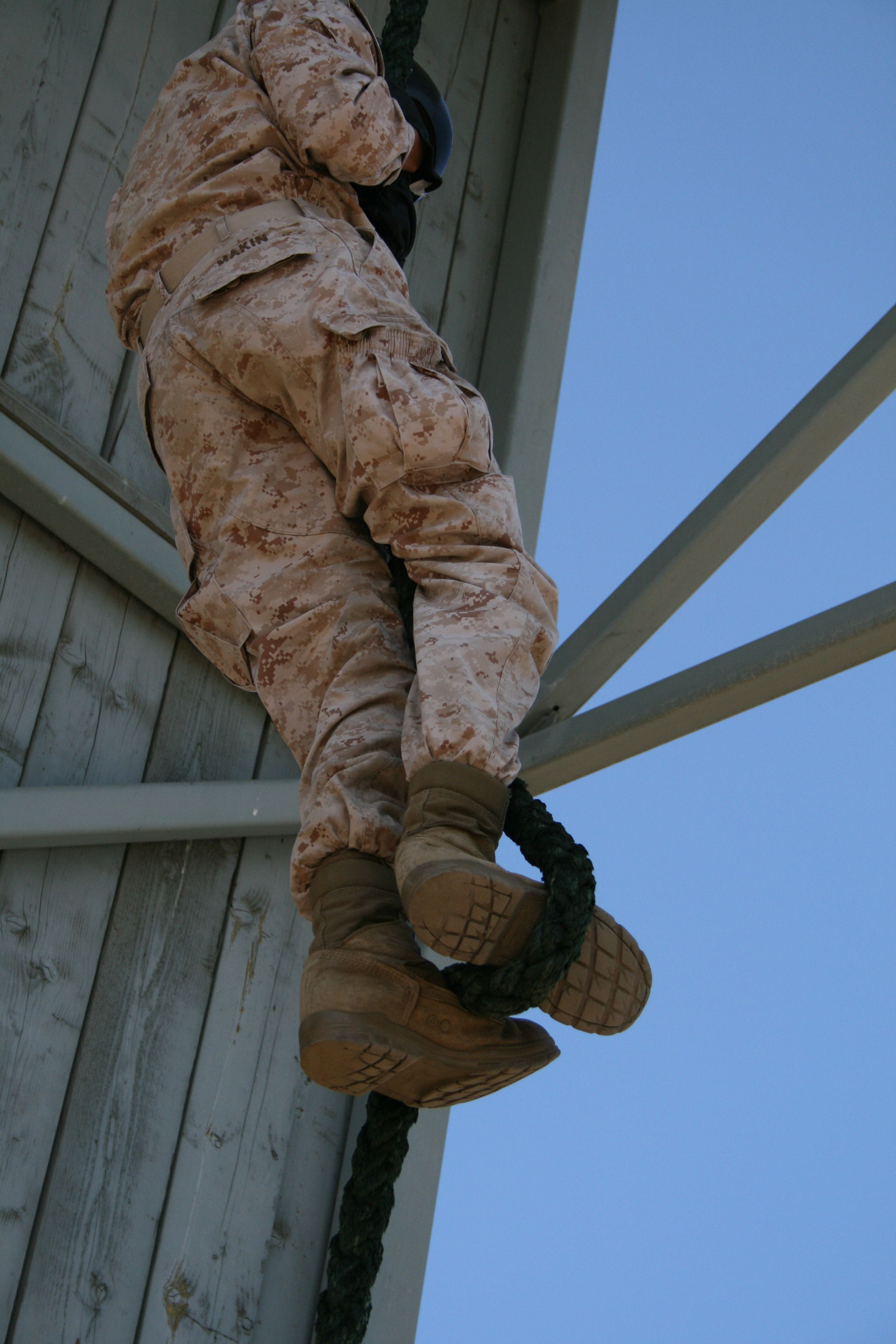
Another area for improvement included the underside of the arch area. Soldiers had to practice slowing down and coming to a complete stop on the rope in case the landing zone was compromised. Standard issue boots did not help to address this need.
We put their standard issue boots to the test with multiple Fast-Rope runs and examined the results. We took note of the areas that wore out the fastest and areas that needed improvement.
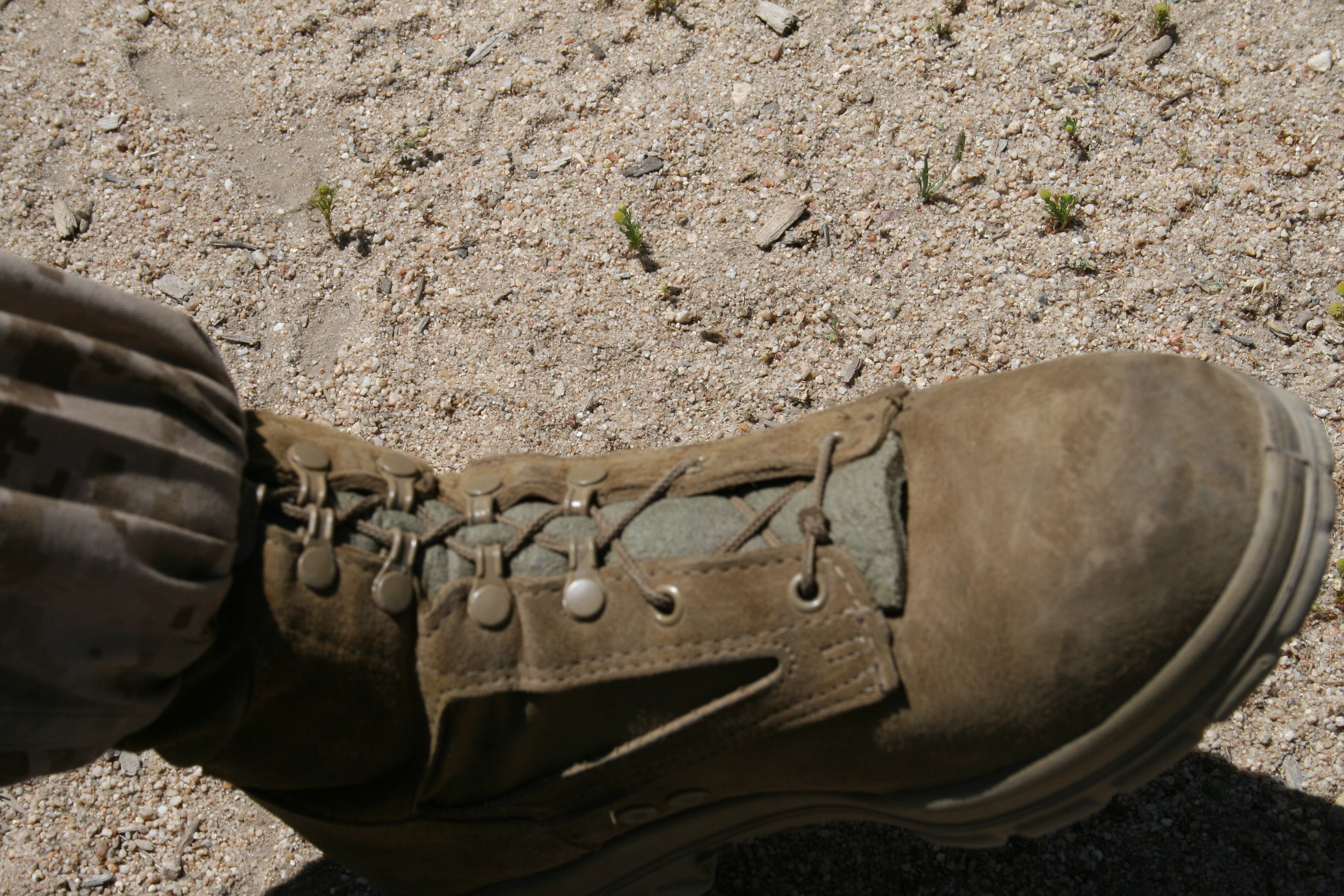
One soldier shared a common problem that was hard to fix in the field. Standard issued laces were too long and became uneven over time. He solved it by tying a knot in the middle of the laces to prevent them from shifting to one side. We thought this solution simple, effective and easy to incorporate.
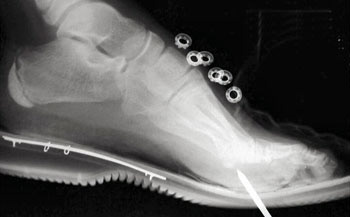
One of the major problems in urban operations was soldiers being routinely injured by stepping on nails. We sought to find a material that would be flexible and puncture proof to help avoid injuries.
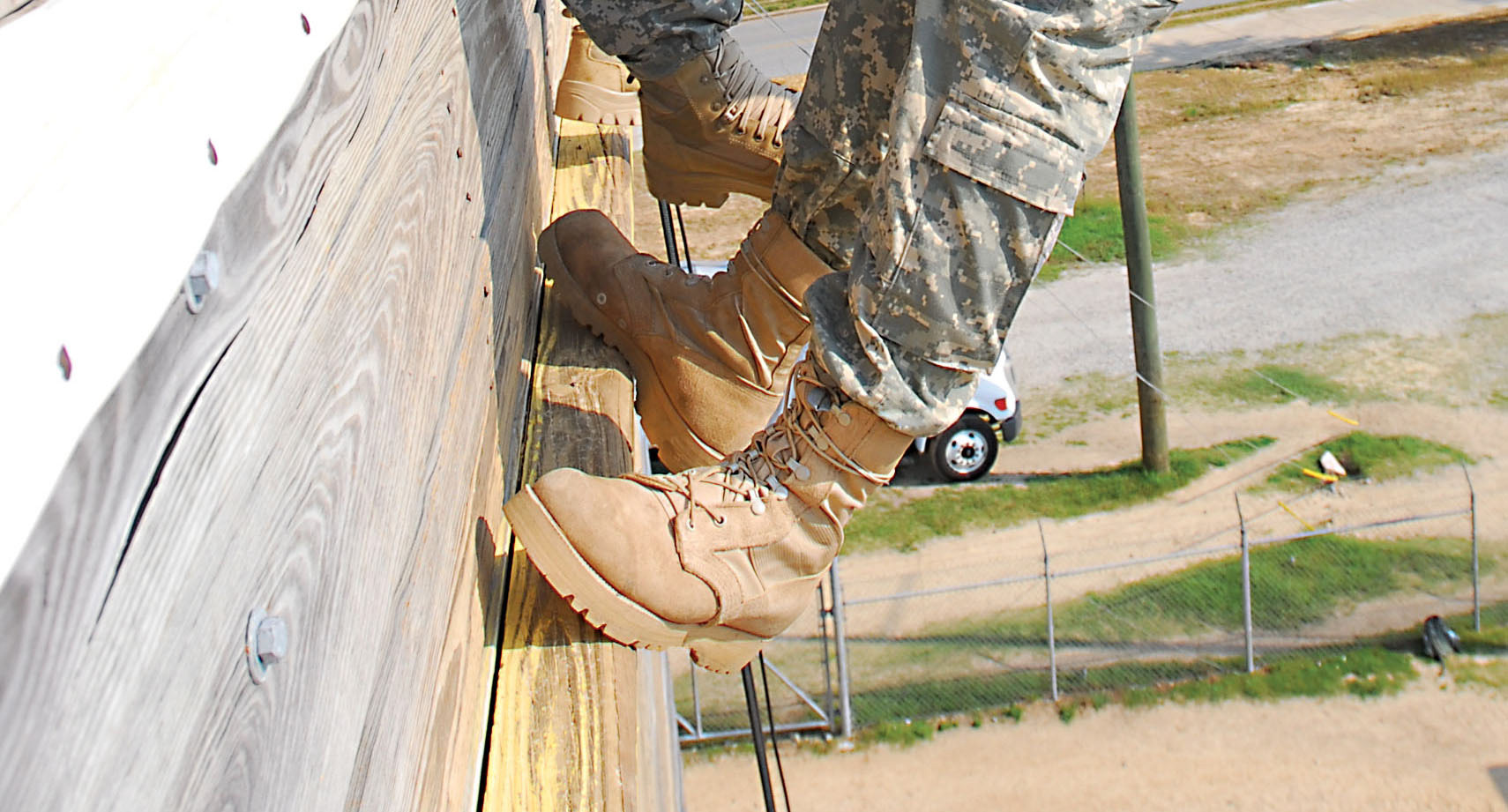
We looked at how to improve the interior medial edge to help rappelling or scaling of vertical walls.
As we delved deeper into research, we looked for other opportunities to improve and solve problems the soldiers faced.
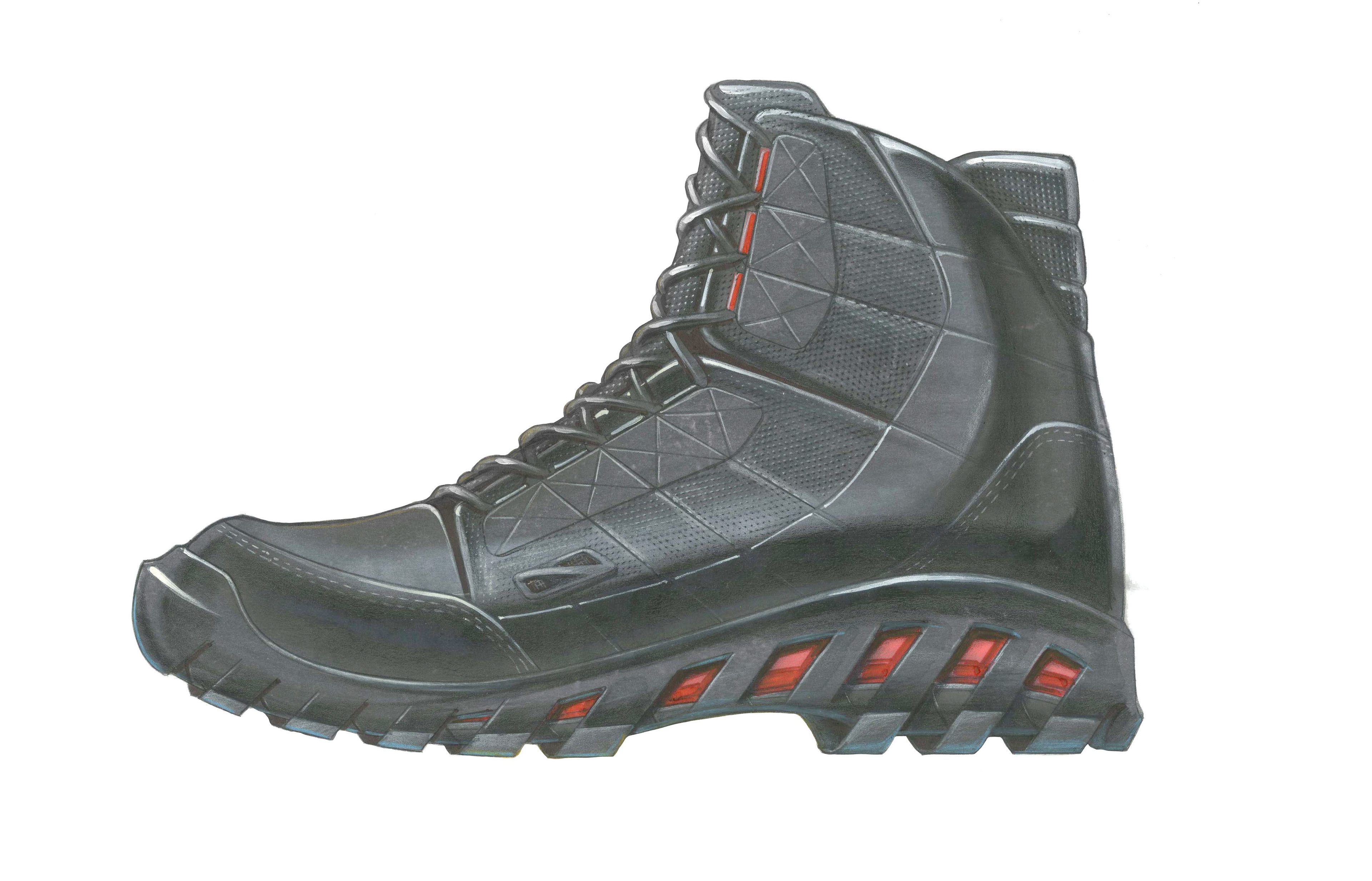
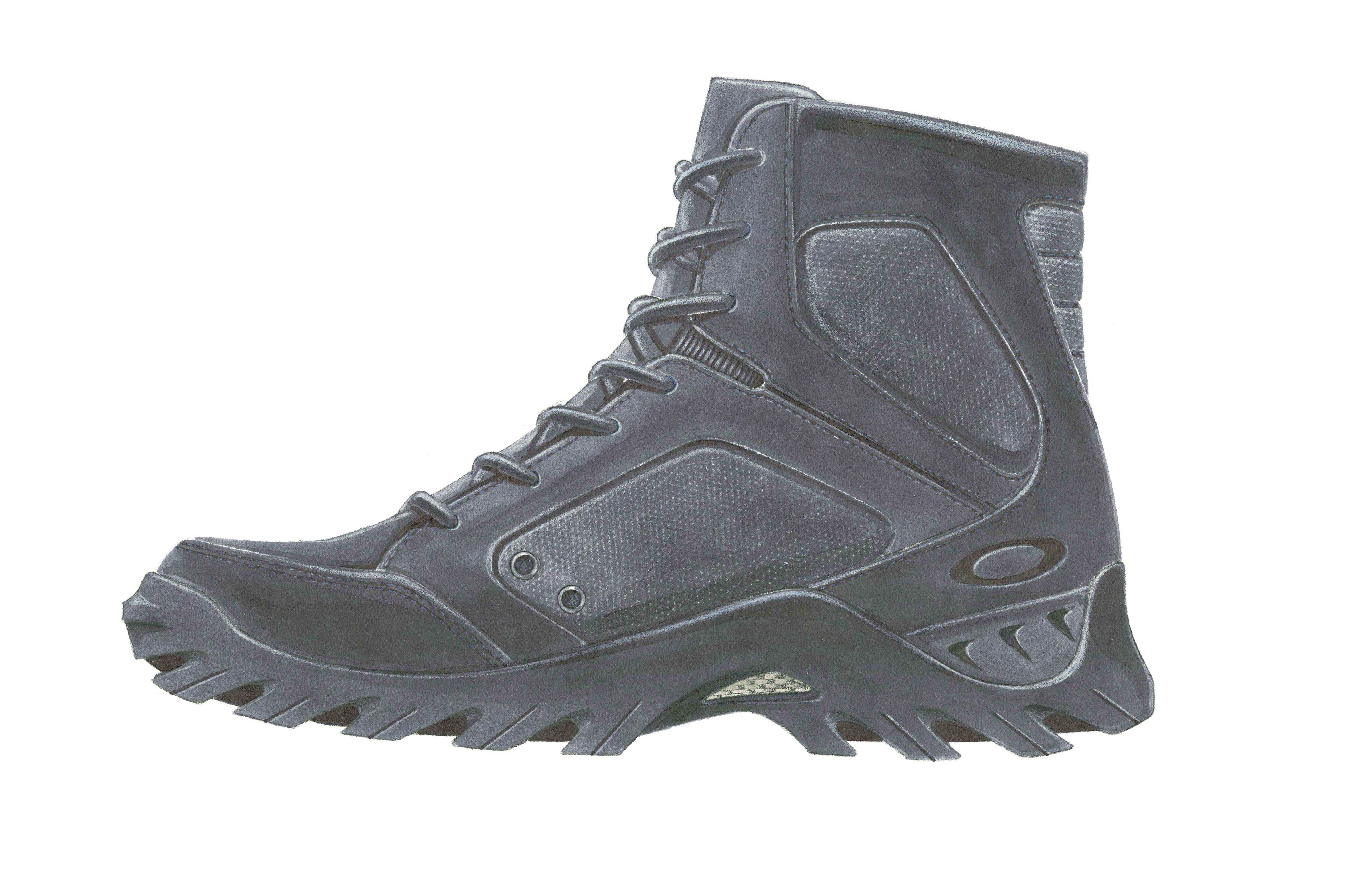
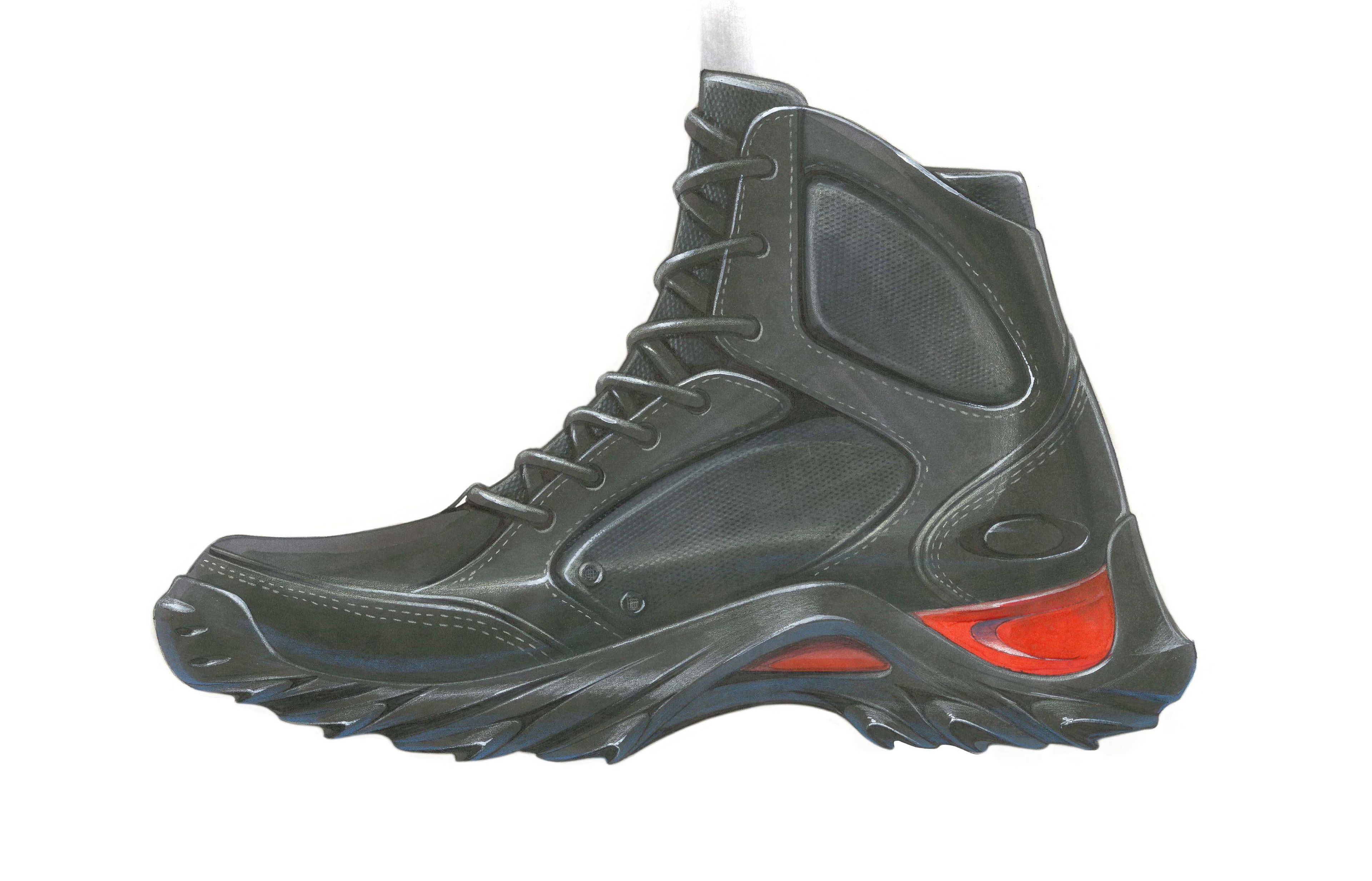
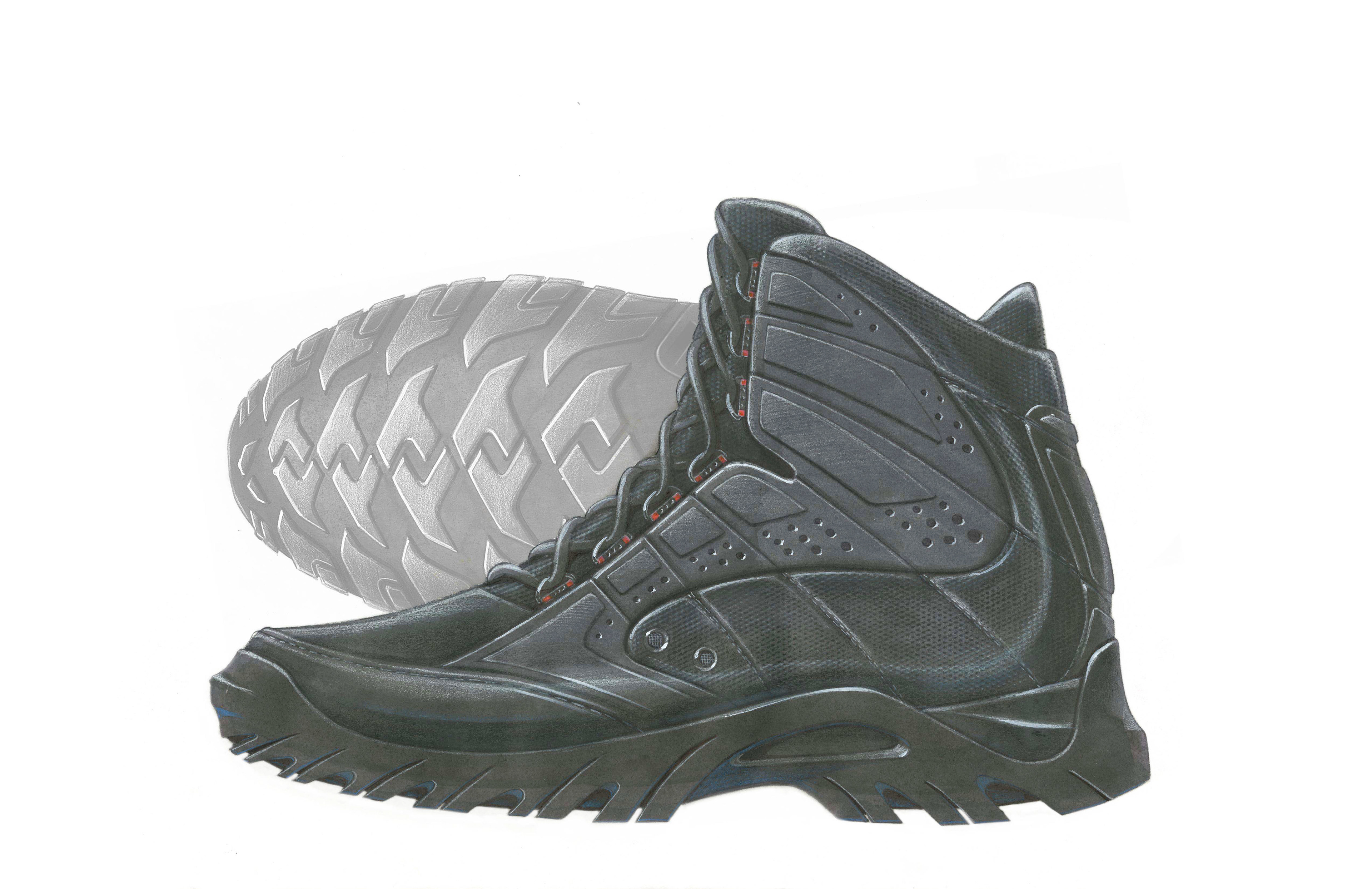
Initial concepts explored exposed EVA outsoles, simplified panel construction, optimized venting ports and alternative lacing systems to help deflect Infrared sensors. Throughout this phase, we kept in mind the military's guidelines on aesthetics and construction as well as Oakley's visual brand identity.
Our final design had an asymmetrical medial side with relocated stitching to prevent premature Fast-Rope abrasion. The side panel was perforated to improve breathability in desert climates.
Each boot came pre-knotted to prevent lace imbalance.
The modified arch piece is made from flexible, ultra high abrasion compound rubber. The rail grip pattern helps the soldier to slow down and come to a complete standstill mid Fast-Rope deployment.
The offset tread pattern was designed to allow for mud and soil to break away from the outsole during flex.
The LF assault boot incorporated new features for Fast-Rope deployment that were new to military footwear. It pioneered asymmetrical wear zones, high abrasion arches and puncture proof soles. The upper was made with highly durable Cordura nylon, 1.6 mm thick split leather and the outsole was made with a specially formulated hydrophobic rubber that had improved grip in wet conditions. All these innovations combined made it one of the most functional pieces of military equipment that Oakley had produced for the armed forces.
SPECIAL FORCES
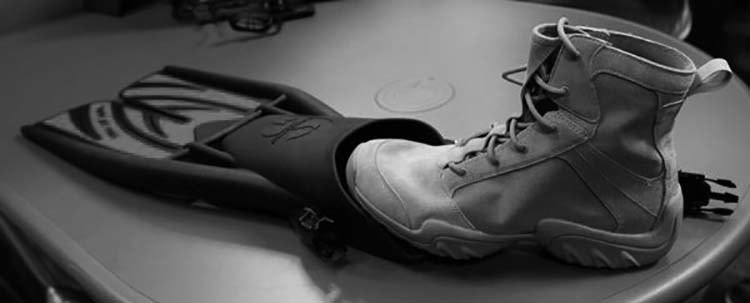
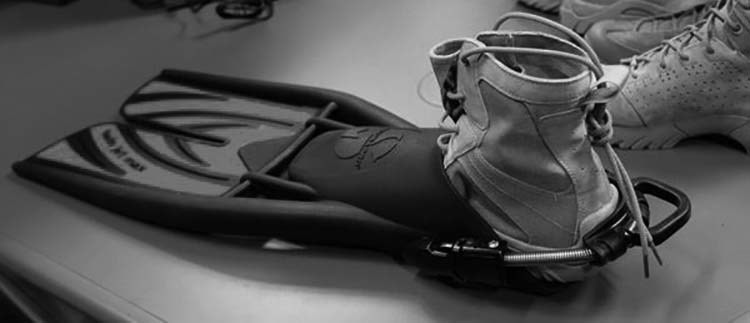
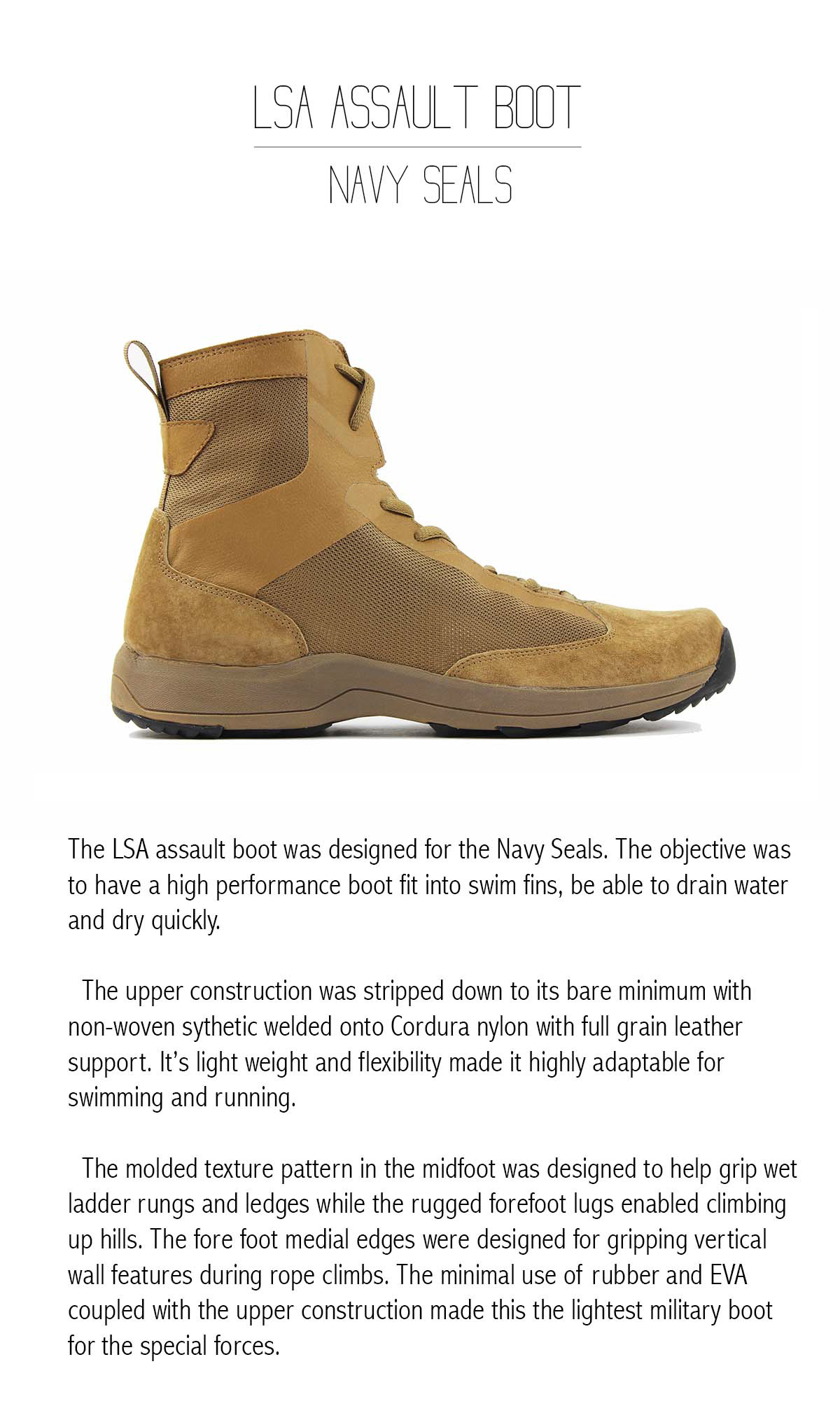
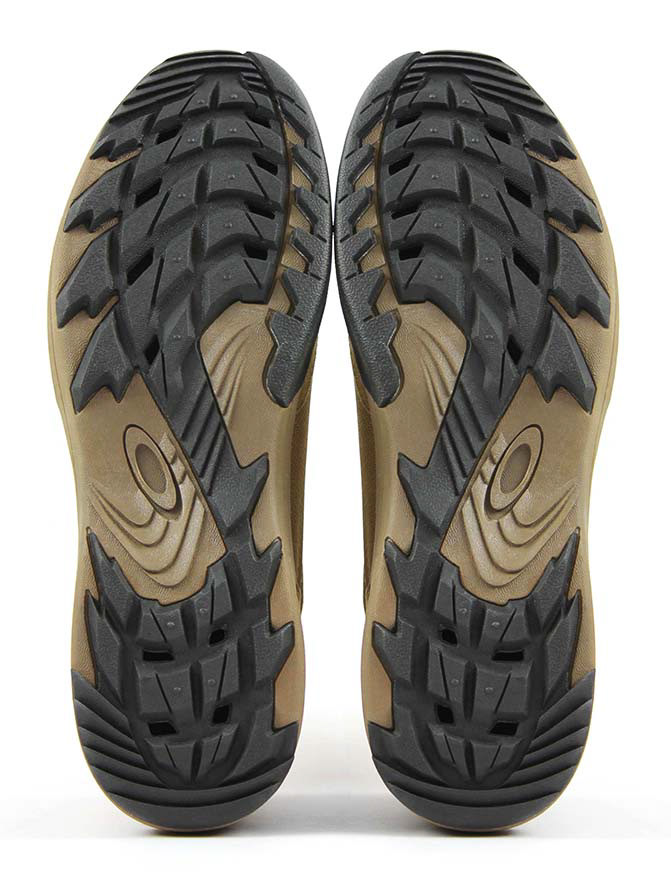